Custom Printed Rollstock
Custom Printed Rollstock
Rollstock Film from Unified Flex Packaging Technologies
Innovation meets efficiency! Our custom extruded and laminated rollstock film offers a versatile and cost-effective solution for your packaging needs. With customization options, exceptional barrier properties, and superior print quality, our rollstock film is designed to elevate your products and enhance brand visibility.
Our custom extruded and laminated films work efficiently with both vertical form fill seal machines and horizontal form fill seal machines. We configure the roll stock film to suit your application and your budget.
All our products are available with the following features:
- Up to 12 color flexographic printing
- Glossy finish, matte finish, or a combination finish material
- Reverse printing and surface printing capability
- Easy to open Poly structures are also available
Rollstock Film Types
Flexible packaging films are often referred to as flexible packaging rollstock or flexible packaging laminates. We supply high-quality flexible packaging rollstock specifically configured for optimal performance based on the needs of our customers with food safety and shelf longevity in mind.
Our packaging specialists work with our customers through every stage of packaging development meeting their expectations and maintaining brand integrity.
Through package engineering, we determine the size, shape, and material composition suitable for desired results. The benefit of being a well-established packaging equipment manufacturer, we can determine packaging material compatibility with the filling equipment.
We have creative in-house graphic designers to assist with all elements of graphic design including prototype and pre-press due diligence.
There are four primary types of laminations, each with key benefits for your business and customers.
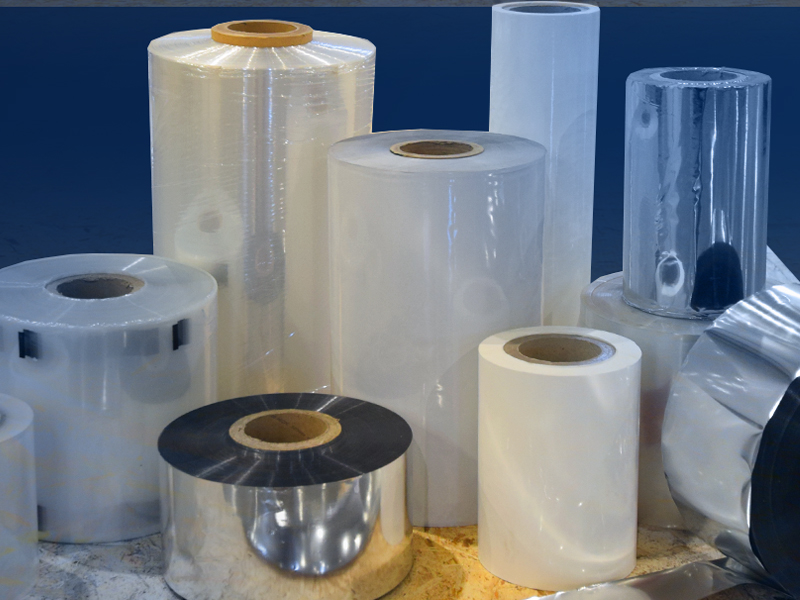
High Barrier Film Laminations
High-barrier film laminations combine multiple layers of film to protect products from moisture, oxygen, light, and other contaminants. The barrier helps maintain the freshness, flavor, and quality of the packaged product.
- Available in foil or clear laminations.
- Ideal where a high barrier is required from oxygen, moisture, and chemicals
- Longer shelf life
- Maximum durability
- Custom poly film extrusions for excellent sealing
- Alox coating, PVDC, HDPE, and EVOH custom extrusions available
Metalized Films Laminations
Metalized film laminations incorporate a layer of metal (usually aluminum) within the film structure. These laminations provide excellent barrier properties, making them highly effective in preventing moisture, oxygen, and light from impacting the freshness and integrity of the products.
- Excellent barrier and bonding properties
- Metalized BoPET films
- Metalized BOPP films
- Metalized Polyester films
OPP Film Laminations
OPP film laminations refer to using Oriented Polypropylene (OPP) film as one of the layers in the lamination structure. OPP film is a type of plastic film known for clarity, strength, and high tensile properties. It has excellent barrier properties, moisture resistance, and heat-sealing capabilities.
- BOPP films and high-strength BOPP films, CPP Films
- Good dimensional strength
- Good stiffness
- Resistance to tear and abrasion
- Cost-effective
Stick Pack Films
Stick pack films refer to specialized packaging materials used for producing stick packs, which are slim, elongated pouches with a narrow width and sealed on both sides. Stick pack films are designed to offer several benefits, including efficient use of packaging material, reduced product waste, and ease of opening and dispensing for consumers.
- Easy tear properties
- Excellent barrier to oxygen and moisture
- Good stiffness properties
- Superior sealing characteristics
- Custom formulations for liquid or powder applications
The Unified Flex Advantage
If you want consistency, minimal waste, and fast operating speeds with your rollstock packaging, you’ve come to the right place. Our value-added package development and quality control processes make our rollstock products top performers in the industry.
Food Safety
- Extensive food safety testing
- High-resolution spectrophotometers for color matching
- Pre- and post-production thickness testing
- Temperature, dwell time, and pneumatic pressure seal testing
- Tensile strength testing
- Consistent friction properties
- Consistent sealing properties
- Consistent barrier protection
- Consistent color printing+
- Reduced downtime
- Minimal to no wastage of film
- Quick splicing of a new roll of film
- Faster operating speeds
- Solvent residue detection
- Microbial detection
- Peel strength detection
- Seal strength detection
- Pressure & drop properties detection
- And more!
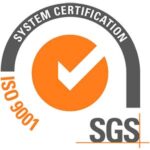
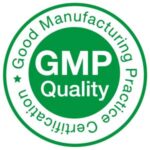
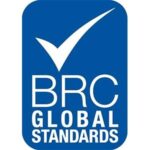
Materials Engineering
We use the highest quality resins manufactured by global leaders such as BASF, Dupont, and Dow Chemicals to extrude our flexible packaging films. All flexible packaging films we produce are customized to match the use and application of the film. Shelf life expectancy is carefully measured by calculating the rate of flow for oxygen and water vapor through the packaging materials. We offer a wide variety of metalized and non-metalized flexible packaging films which can be configured in various compositions to formulate the appropriate packaging material for the application. Our chemical engineers bring decades of formulation experience for food packaging applications maintaining the aroma, taste, and physical properties of the food products. We also specialize in co-extruded LLDPE & HDPE films. Co-extruded films can be used as stand-alone films or in laminated structures to provide excellent sealing properties to the package.
Color Management
Achieving desired colors on flexible packaging products is imperative for great shelf appeal. A properly printed package attracts the attention of the eye and results in more sales for the product. Our flexible packaging printing equipment uses inline high-resolution spectrophotometers to measure and monitor the color data. This system helps us generate the exact colors required for printing. It can quantify colors equally well on high gloss surfaces as well as metalized shiny surfaces. This results in efficiently matching the printed colors closest to the specified colors on the computer-generated artwork. This process also makes our manufacturing process more efficient and reliable and helps reduce the cost of printed products. An offline high-speed inspection machine also checks the quality of the printed film and splices out any inconsistencies in printing quality.
Quality Control
Our goal is to achieve 100% customer satisfaction by providing reliable, consistent & high quality flexible packaging products. We have developed strict quality control mechanisms that measure all aspects of flexible packaging products from receiving raw materials in our manufacturing facility to the final packaging and shipping of goods.
COF Detection
On high speed film converting and printing machines the static friction coefficient of the film is a major factor in determining the performance characteristics of the film during production. COF is also important to monitor and maintain as the flow properties of flexible packaging materials change with a change in COF, potentially causing disruptions in packaging equipment. Unified flex evaluates friction coefficient according to ASTM D1894 standards.
Thickness Detection
The thickness of flexible packaging films determines the clarity, durability, and flexibility of the films. As thickness increases, clarity and flexibility reduce while the durability of the film increases. Pre and post-production tests are performed using a mechanical micrometer. Flexible packaging films with consistent thickness do not overstrain and stretch during the printing process resulting in superior print quality.
Sealing Test
Heat sealing is the most popular method of welding plastic materials. One of the most important characteristics of flexible packaging materials is the sealing properties of the film. All films are tested under specific temperature, dwell time, and pneumatic pressure. The sealing strengths of the flexible packaging films are measured according to the ASTM 882 standards.
Tensile Strength
Tensile strength is the maximum mechanical stress a packaging material can withstand without breaking. We test our films for tensile strength as its an important property of the flexible packaging material. This test can determine the peel force, tear force, elongation rate, puncture resistance and adhesive strengths of the films. Unified flex ensures compliance with requirements on strength characteristics in accordance with ASTM 882 standards.