Packaging Gel Packs: Overcoming the Challenges of Temperature-Controlled Logistics
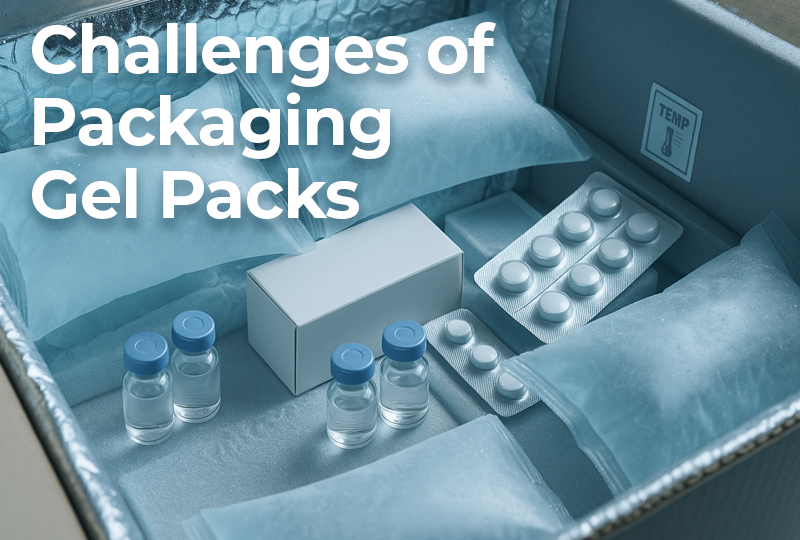
Temperature-controlled packaging plays a critical role in industries ranging from pharmaceuticals to food logistics. Gel packs are often relied upon to maintain these temperatures, ensuring that products like medicine, fresh food, and cosmetics arrive in optimal condition. However, packaging gel packs come with their own set of challenges; issues that can compromise the effectiveness of the product and create inefficiencies in the supply chain.
In this article, we’ll dive into the unique challenges of packaging gel packs and explore how the right materials and technology can help businesses overcome these obstacles. We’ll also discuss how the right packaging choices can align with your sustainability goals, ensuring that your temperature-controlled products are not only safe and efficient but also environmentally responsible.
The Unique Challenges of Packaging Gel Packs
Gel packs are essential in the cold chain logistics process, but their packaging isn’t always as simple as it seems. Here are the key challenges faced by manufacturers:
1. Moisture Management and Maintaining Cooling Power
Gel packs are designed to maintain specific temperatures during transit. However, when exposed to humid environments, condensation can form on their surfaces. While this surface moisture doesn’t reduce the gel’s internal cooling capacity, it can affect packaging materials, labels, and product presentation. To mitigate these issues, many cold chain operations utilize “no-sweat” gel packs, which feature multi-layered exteriors that absorb surface moisture, ensuring that moisture-sensitive products arrive in optimal condition.
2. Inconsistencies in Shape and Size
Gel packs come in a variety of sizes to meet different shipping requirements. However, variations in filling or sealing processes, especially in lower-volume or manual operations—can lead to slight inconsistencies in shape and size. These irregularities can make packing less efficient, wasting valuable space in cartons or coolers. They can also disrupt consistent temperature distribution by creating air gaps. Packaging methods need to be flexible enough to handle these variations while ensuring every gel pack delivers reliable cooling performance in transit.
3. Leakage and Contamination Risks
Gel pack packaging carries an inherent risk of leakage if not properly designed and handled. Using the wrong film material, poor sealing practices, or rough handling can cause packs to rupture, resulting in leaks that contaminate other goods and damage packaging. This risk is especially critical in sensitive industries like pharmaceuticals and biotechnology, where maintaining sterility and temperature control is essential. As a result, preventing leakage and contamination is a top priority in gel pack packaging design and process planning.
4. Sustainability Concerns in the Cold Chain
Gel packs, although effective for temperature control, present a sustainability challenge due to their single-use nature. In an age where sustainability is a growing concern, reducing the environmental impact of packaging has become a top priority. While gel packs are reusable in some cases, many end up as waste after a single use, contributing to unnecessary environmental strain. The key lies in finding packaging solutions that are both functional and environmentally responsible.
Best Practices for Packaging Gel Packs: Materials That Work
To ensure gel packs maintain their cooling properties and reach their destination intact, high-quality materials and packaging techniques are essential. Here are the best practices for packaging gel packs effectively:
Best Packaging Materials for Gel Packs
- High-Barrier Films:
High-barrier films protect against moisture, oxygen, and light, preserving the integrity of gel packs during storage and transit. They help prevent leaks and maintain cooling performance by ensuring the gel stays contained and effective.
- Foil Pouches:
Foil laminates provide exceptional barrier protection, keeping external moisture and contaminants out. Their airtight sealing capability makes them ideal for demanding cold chain applications.
- Resealable Pouches:
While not always used in large-scale shipping, resealable pouches can be valuable for gel packs intended for reuse in internal logistics or lab settings. They help maintain integrity between uses and reduce waste.
- Vacuum Packaging:
Vacuum-sealed secondary packaging can eliminate air gaps around gel packs, improving contact with products and maintaining consistent temperatures during transit. This method enhances overall shipment efficiency, even if the gel pack itself isn’t vacuum-sealed.
Ineffective Packaging Solutions
- Basic Polyethylene Bags:
Low-barrier PE bags offer minimal protection and are prone to puncture or poor sealing. Without robust seals, they risk leaks and reduced effectiveness during shipping.
- Non-Sealed Pouches:
Improperly sealed pouches expose gel packs to environmental factors like humidity and physical stress, increasing the risk of leaks and contamination.
- Low-Quality Pouches:
Weak or thin materials can tear or puncture easily, compromising containment and increasing the risk of damage to other products in the shipment.
How the VFFS Vertobagger Falcon Solves Gel Pack Packaging Challenges
The VFFS Vertobagger Falcon is specifically designed to address the unique challenges of packaging gel packs efficiently. Here’s how it solves these issues:
1. Servo-Controlled Precision for Consistent Bag Formation
The Falcon’s servo-driven pull belts and electronic vertical seal alignment work together to maintain precise, consistent film control throughout the packaging cycle. This ensures that every gel pack is formed with uniform dimensions and alignment, reducing variability and supporting smooth downstream handling. By keeping bag formation precise and repeatable, the Falcon helps eliminate waste and ensures that production stays efficient, even at higher volumes.
2. Reliable Pneumatic Sealing for Leak Prevention
Equipped with a pneumatic horizontal sealing system, the Falcon creates strong, reliable seals that are essential for gel packs containing liquid or semi-viscous contents. This robust sealing technology prevents leaks and moisture infiltration, keeping the cooling gel securely contained throughout storage and transit. For temperature-sensitive shipments, this dependable seal integrity is crucial to maintaining cold chain standards and protecting product quality.
3. Versatile Bag Forming Capabilities
Gel packs require packaging that can adapt to a variety of shipping and handling requirements. The Vertobagger Falcon is designed to produce pillow bags that can be tailored for different applications; offering options like side gussets for added capacity or Euroholes for retail display and easy hanging. This flexibility allows manufacturers to select the most practical configuration for their cold chain needs, ensuring secure, efficient, and market-ready packaging for pharmaceutical, food, or cosmetic products.
4. High-Speed Operation with Intuitive PLC Control
With production speeds of up to 100 bags per minute, the Vertobagger Falcon significantly increases throughput compared to manual packaging methods. Its PLC control system with a user-friendly touchscreen interface allows operators to easily set and adjust parameters for different gel pack sizes and formats. This combination of speed and control enhances productivity while maintaining the precision required for temperature-sensitive packaging.
5. Cost-Effective Film Handling System
The Vertobagger Falcon’s pneumatic film locking system ensures secure, consistent film feeding throughout production runs. This reliable film handling ensures smooth operation and consistent bag formation, which is crucial for gel pack manufacturers who require dependable seals and well-formed packs. By reducing manual adjustments and downtime, the Falcon helps improve overall production efficiency while supporting high-quality, reliable packaging for cold chain applications.
Why Investing in the VFFS Vertobagger Falcon Makes Sense for Gel Pack Packaging
Meet Growing Demand with Efficient Gel Pack Packaging
As demand for temperature-sensitive products rises, businesses need packaging solutions that deliver both efficiency and precision. The Vertobagger Falcon is built to meet this challenge, providing the scalability needed to keep pace with market demand while ensuring gel packs maintain their integrity. Its customizable configurations and ability to handle diverse film types let operations adapt to evolving requirements without sacrificing quality or throughput.
Reduce Costs and Improve Profitability
The Vertobagger Falcon’s automated operation reduces labor costs significantly compared to manual packaging. Precise control systems minimize film waste and lower the risk of rejected packs due to sealing issues. This consistency improves production planning and inventory management. For gel pack manufacturers, the result is lower operating costs and better profit margins—a sound investment for growing temperature-controlled logistics.
Sustainability Without Compromising Performance
Environmental considerations are essential in packaging decisions. The Vertobagger Falcon supports these goals through efficient material use and compatibility with eco-friendly films. Precise film measuring and cutting minimize waste, while advanced sealing technology ensures that even sustainable materials maintain the necessary protection for gel packs. This balance of operational effectiveness and environmental responsibility helps businesses meet compliance targets and strengthen their brand reputation.
Future-Proof Your Gel Pack Packaging
The Vertobagger Falcon offers gel pack manufacturers a practical way to meet growing demand while improving operational efficiency and sustainability. With its automated operation and adaptable design, it helps teams reduce costs, maintain consistent quality, and stay ready for changing market requirements.
Ready to learn more?