Why Cold Chain Teams Are Switching to Pillow Bags for Gel Pack Packaging
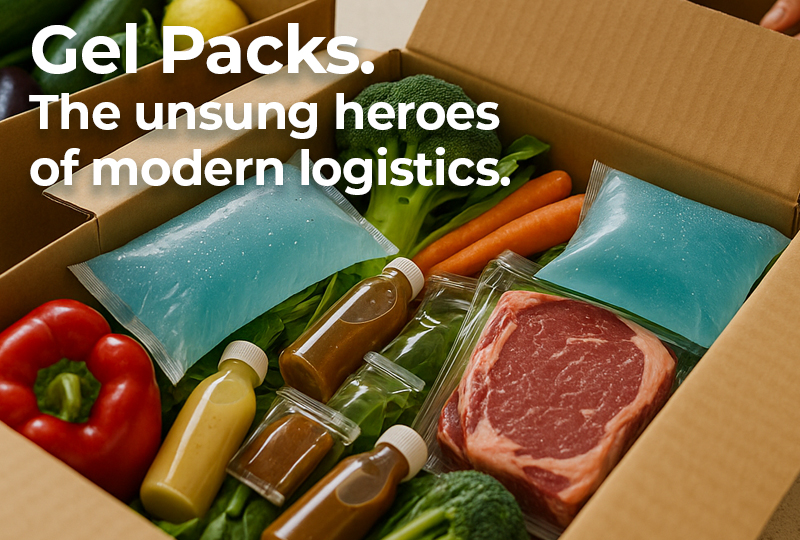
The biggest changes in logistics rarely come with a fanfare. They start with a quiet shift, a pilot run, a test line, and gradually redefine what’s considered standard. That’s what’s happening right now in gel pack packaging.
The gel packs themselves are fine. They’re essential, reliable, reusable, and crucial to cold chain logistics. But the way many teams still package them? That’s where cracks are beginning to show.
Manual handling, oversized poly bags, and inconsistent seals may have worked in the past. But as shipping volumes rise and fulfillment timelines compress, those methods are hitting their limits. More operations teams are stepping back, re-evaluating the process, and shifting to a format that better supports scale.
The Hidden Cost of Familiar Packaging
For many operations, gel pack packaging still relies on hand-filled, heat-sealed cut film or oversized stock bags. It’s familiar and that’s part of the problem.
This approach slows things down. Manual workflows limit throughput. Seal consistency varies from pack to pack, introducing risk. And excess film waste, often overlooked, quietly inflates cost and environmental impact.
These aren’t dramatic failures. They’re subtle inefficiencies that build over time. They slow lines, increase labor dependency, and make packing out and palletizing less predictable. As one operation lead at a national meal kit company put it, “The gel packs did their job, but the packaging created delays and inefficiencies.”
That sentiment is becoming more common, especially in high-growth sectors where demand is outpacing the process.
When Growth Outpaces Packaging
Cold chain logistics is scaling quickly from meal kits and frozen pet food to vaccines and diagnostics. According to Persistence Market Research, the global gel pack market is projected to hit $1.82 billion by 2032. The broader cold chain market? It’s forecast to reach $932.70 billion by 2033, according to the IMARC Group.
That kind of growth isn’t abstract; it’s operational pressure. More units, faster turnaround, tighter margins. And the packaging systems that work for small runs can quickly become bottlenecks when volume spikes. Gel pack packaging methods that rely on manual labor or excess material waste are among the first to break under that pressure.
Cold chain leaders are looking at every input; labor, materials, throughput to find gains. That often leads them to reconsider the packaging format itself.
Why Pillow Bags Are a Smarter Fit
Pillow bags aren’t new, but their use in gel pack packaging is rising because they solve the problems that legacy methods create. Produced using vertical form fill seal (VFFS) machines, pillow bags bring repeatability, speed, and efficiency to a process that’s historically been manual and messy.
Because the bags are formed, filled, and sealed in one motion, they eliminate inconsistencies in seal strength and shape. That reduces leakers, cuts down on rework, and ensures each pack has a uniform footprint, critical for stacking and secondary packaging.
They also minimize material waste. Instead of relying on oversized or generic bags, operations use only the film necessary for the volume of gel, supporting both sustainability and cost control.
Most importantly, pillow bags integrate cleanly with automation. That unlocks higher throughput and more consistent output, without increasing labor or complexity.
Where It’s Working Already
Across industries, pillow bags are gaining ground in cold chain operations.
Meal kit providers use them to ensure pack consistency across hundreds of thousands of shipments. In diagnostics and pharma, where leakage isn’t just an annoyance but a risk, pillow bags provide clean, dependable seals. And in frozen and chilled pet food, teams appreciate the way pillow bags hold their shape, reduce mess, and simplify palletization.
Some manufacturers are even using pillow bags for specialized cooling media, such as ice bricks or phase-change materials, because the format is flexible enough to handle different viscosities and fill volumes.
What these teams have in common is simple: they’ve found that changing the package can improve the process.
One Format, Many Films and Why That Matters
A pillow bag is only as reliable as the film it’s made from. For gel pack packaging, that means choosing materials that can handle freezing temperatures, compression during shipping, and long transit times, without cracking or leaking.
The right film helps ensure strong, consistent seals, reduces the risk of leaks, and protects the integrity of every shipment. It’s not just about appearance or cost, it’s about performance when it counts.
Films designed for cold chain use often include high-barrier laminations that block moisture and oxygen, foil structures for maximum protection, and metalized or clear multilayer films engineered to stay flexible even in sub-zero conditions. Choosing the right type depends on your needs for barrier strength, sealing reliability, and compatibility with your equipment.
To get it right, teams should prioritize films specifically formulated for cold chain conditions and test them under real production and storage scenarios. That way, they can be confident their packaging will hold up to the customer.
How Unified Flex Supports Scalable Gel Pack Packaging
We’ve engineered our vertical form fill seal systems, including the VFFS Vertobagger Falcon, with gel pack packaging in mind. These machines deliver strong, repeatable seals and high-speed performance while accommodating a wide range of bag sizes and fill volumes.
The systems are designed to integrate easily into your production line working seamlessly with fillers, conveyors, and more. And thanks to intuitive interfaces and fast changeovers, operators can stay focused on output, not troubleshooting.
Whether you’re running a pilot or scaling round-the-clock production, the equipment adapts to your pace.
From Pilot to Proof: A Smarter Way to Scale
Change doesn’t have to mean disruption. In fact, many of our customers start with a single test line.
They use it to evaluate new pack formats, compare materials, measure labor impact, and verify throughput. When the data shows it’s working, the transition from trial to scale becomes a logical next step, not a leap of faith.
Packaging That’s Quietly Driving Results
Packaging rarely gets the spotlight, but in cold chain operations, it quietly determines success. It prevents delays, protects integrity, and keeps fulfillment moving.
That’s why more operations teams are switching to pillow bags. They make gel pack packaging simpler, faster, and more predictable. And as volume grows and expectations rise, those gains turn into strategic advantages.
If your current setup is starting to show its age, we’d be glad to help you explore what’s next. Let’s talk about what a pilot could look like and how we can help you build a better packaging system, one pack at a time.